Environmental responsibility
towards an increasingly green future

Eco-sustainability: a choice, a reality.
The reduction of the environmental impact, deriving from production, occurs through a series of processes that include:
- Control of emissions;
- Efficient use of energy, water and raw materials;
- Reduction and recycling of packaging;
- Correct waste disposal;
- Optimisation of logistics;
- Collaboration with local suppliers.
Fami entrusts to a single technical department, with young and creative personnel, the search for increasingly functional and innovative materials and products, adopting the most up-to-date three-dimensional simulation programmes and production technologies with a low environmental impact.
Safeguarding our surroundings
Environmental protection begins from a small but important step: the installation of a photovoltaic plant on the roof of industrial sheds. Some 6,140 polycrystalline silicon panels occupy an overall surface of 9,824 m2 and ensure high levels of quality and performance stability.
The photovoltaic plant produces 24% of the company’s annual requirements and affords numerous advantages: saving of fossil fuels, use of the sun and thus of a ‘clean’ and inexhaustible energy source, less dispersal of the electricity generated and immediately used, minimal operating and maintenance costs.

625.000 kg* of CO2 saved each year

24%* of clean energy

17.000 trees* saved each year
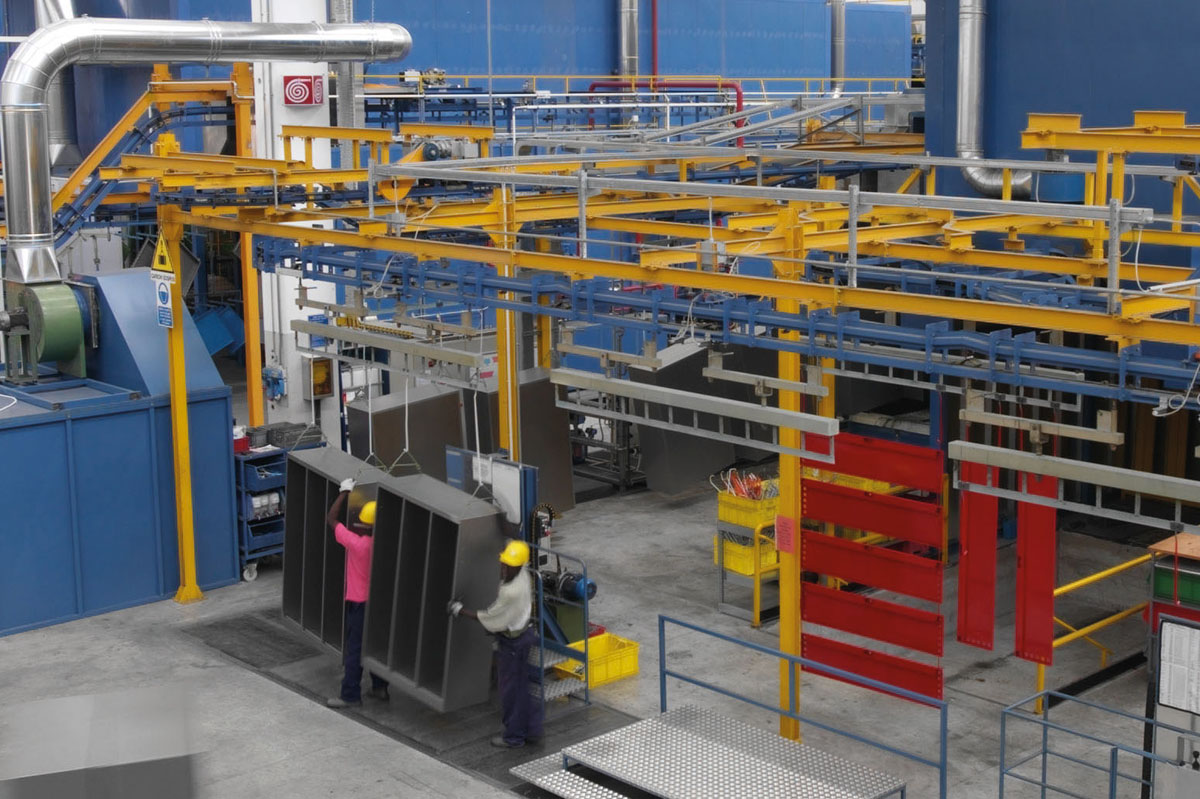
235.000 kg* of coal saved each year
* indicative average values as from 2011.
New life for rejects
Helping the environment means giving new life to rejects produced daily. Fami has implemented procedures for reusing materials in the coating, wood, polystyrene and paper departments.
Coating
The process for reusing raw materials involves both the actual paint and the water used for the product washing process.
Powder coating -> 2–3% of reject material, thanks to the suction of powder and its re-introduction into the coating plant through falling (80–90% recovery).
Product washing -> a series of tanks for the pre-coating wash. The successive tank uses the water of the previous tank, and so forth. The water of the first tank is totally discarded because it is too dirty.
Production of demineralised water -> two plants. The first plant generates 30% of waste water which is then used to wash the coals of the second plant. Result: from 10,000 litres of water discarded each month we obtain 5,000 litres every two months.


Wood, polystyrene, paper
Rejects are recovered to produce new raw materials which are then used in the production cycles of customers. Roughly 321,880 kg of pallets and 5,360 kg of polystyrene are collected annually from two local companies to create new products to be introduced in the market.
The wood used to manufacture our products and part of the paper used to print the catalogues are purchased from companies with FSC® (an international non-governmental organisation set up to promote the responsible management of forests and plantations) certification.
Regarding the packaging, the boxes are made by companies adhering to GIFCO (Italian Group of Corrugated Cardboard Manufacturers) which manufactures cardboard with 80% of recycled fibres and uses natural glues and water-based colours for printing.